Nike, Inc. (NYSE:NKE), better known for its design and marketing, is quietly undergoing a manufacturing transformation. Using independent contract manufacturers from around the world, Nike hasn't always wanted to highlight the production part of its business, especially given it was once a poster child for lack of corporate responsibility, allegedly using factories with sweat-shop-like working conditions. After years of benefiting from low-cost foreign labors, Nike seems to have turned to a more technology-based manufacturing process to reduce overall costs and be the next value driver.
Nike has dubbed its corporate initiative for manufacturing revolution as the ManRev project, which receives funding as part of the company's capital expenditures. Nike invested $1.143 billion in property, plant and equipment during its fiscal 2016 ended on May 31, compared to $963 million for fiscal 2015 and more than doubling the amount of capital expenditures from five years ago in fiscal 2012. Most of the investments are related to developments of contract-manufacturer supply chain and corporate initiatives, including the ManRev project.
Nike is undoubtedly in a period of business transition to transform its manufacturing process. By innovating the role of technology in manufacturing, the company aims to reinvent what a footwear factory should look like and how footwear can be best made. One such technological innovation is the so-called Nike Flyknit, a new way of making a shoe upper by knitting or stitching threads and strands to shape and form the upper with computer-controlled precision. This replaces the age-old shoe-making technique of stamping out patterns of uppers in a piece of fabric, which requires cutting and sewing, resulting in a lot of wasted, unused scraps.
According to Nike's own estimates, "Flyknit reduces waste by about 60% on average compared to cut and sew footwear, and through spring 2016, has reduced nearly 3.5 million pounds of waste since 2012." This has direct implications on the company's product cost savings. During the four years since 2012 when Nike first introduced Flyknit, the rate of increase for its cost of revenue trailed the revenue growth rate each year, contributing to the company's continued expansion on gross margin, which was 46.24% at the end of fiscal 2016.
The gross margin expansion was also the result of Nike's ability to command higher prices by delivering innovative, premium products, and the Flyknit's computerized knitting process is becoming a key technological source to help Nike further solidify its product edge. Flyknit's computer-aided knitting process enables designers to micro target each thread of an shoe upper to deliver engineered support that scientifically meets the exact specifications of athletes. This is a highly customizable design and production process that Nike can put into best use to sustain its product differentiation to tilt the price-to-value equation to its favor.
In addition to cost savings and customized design, the third aspect of Nike's Flyknit-based manufacturing transformation is that the production process is changing from being very labor intensive to mostly machine operated. Using Flyknit, human does the shoe upper design, feeds it into a knitting machine with sophisticated software and then, the machine physically makes the product. Shoe factories used to need intensive labors for cutting materials and stitching everything together based on different designs, a major cause for Nike's hunt for cheap labors with outsourced manufacturing.
Despite its worldwide brand recognition and faster growth in certain overseas markets, the U.S. still provides Nike with the single, largest consumption of its products, generating sales in fiscal 2016 more than two and half times of what was for its next largest market, western Europe. One unintended or at least unstated benefit as a result of Nike's manufacturing revolution could be the opportunity of reshoring, that is, moving back some of the company's production back to the U.S. when the need for intensive labors is giving way to machines operations.
This can be in the interest of the company and its shareholders. With manufacturing close to where the market is and responsive to what consumers are buying, local productions help improve supply-chain agility for small, frequent batches of orders. In 2016, Nike stock had its first yearly decline since 2008, breaking up a seven-year stretch of annual share increases, but the stock could easily bounce back once the company's manufacturing revolution takes hold with all the associated benefits translated into better sales and earnings.
Disclosure: I/we have no positions in any stocks mentioned, and no plans to initiate any positions within the next 72 hours.
I wrote this article myself, and it expresses my own opinions. I am not receiving compensation for it (other than from Seeking Alpha). I have no business relationship with any company whose stock is mentioned in this article.
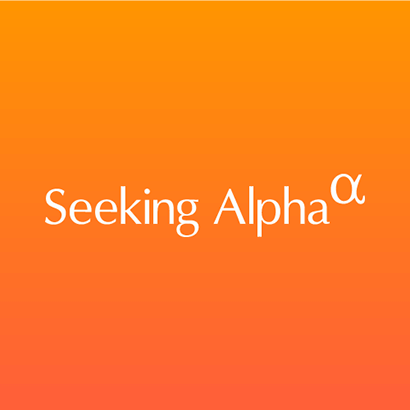